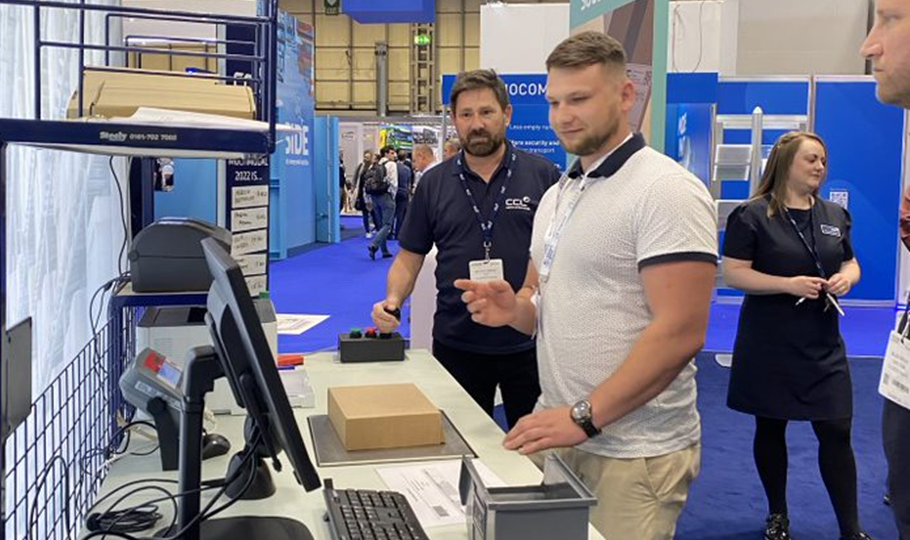
As we get ready to bring our Pack Station Challenge to Multimodal, CCL’s Content Marketing Manager, Julie Shennan examines how our Pack and Dispatch Solution can not only increase the speed of throughput but also reduce error.
The Results
Visitors to Multimodal last year discovered CCL’s Pack and Dispatch Solution can process goods so quickly that they go from the tote, to being scanned, boxed and labelled for dispatch, in as little as 15 seconds.
Although this record speed was achieved in an exhibition demo (The Pack Station Challenge), it shows the pack and dispatch benefits possible to workplaces when you partner with CCL.
In fact, luxury hamper provider Ardtaraig noted that they had saved 8 hours per day, since they started using CCL’s Dispatch Solution.
Peter Mortimer, Director at Ardtaraig said: “CCL helped us ship circa 5000 shipments in the 10 days prior to Christmas. We have been using myCCL for quite a long time now and love the service.”
With such results, you’ll be wondering how the Pack and Dispatch Solution works.
Pack
myCCL, our Transport Management System, connects with your WMS or ERP to allow order data to flow between the two. When you scan a pick list, myCCL loads the whole order on the Pack Bench computer.
Next, you select the type of container you will use to ship the items and the quantity (for example, it might show 2 medium parcels).
Following this, myCCL will send a Box Label to the printer, which is numbered to correlate with the Delivery Note (for example, parcel 1 of 2 parcels).
Then you put the parcel on the scales, scan the barcode of each item, and pack it.
The scales will auto-update the weight of the order as you pack the goods. The scales calculate precise shipment weights, as required by the carrier when booking deliveries, which means fewer disputes or additional charges.
Should you scan the wrong item, an error message will pop up, preventing you from completing the process until the correct one is scanned.
These safeguards stop you putting the wrong items in an order. They are so effective that Manufacturer Swagelok Scotland noted it achieved 100% pack accuracy, since implementing SIMPLE (a CCL Pack and Dispatch Solution).
Peter O'Connor, Former Managing Director at Swagelok Scotland said: “Personally I would recommend it to anybody. I’m very happy, our stores team are very happy, and our customers are very happy.”
Dispatch
Once your order has been fully packed and weighed, myCCL applies pre-set Business Rules, to choose the best carrier for your parcels.
These Business Rules are preferences that you establish upfront, with guidance from CCL, to ensure that you select the shipper best suited to move each type of item, based on budget, deadline, weight, size, destination or customer delivery preference.
After just seconds of running the Business Rules, myCCL will select the carrier and send their delivery labels to your warehouse printer, ready to be stuck on your parcels.
Then the Contents List will print, showing a list of SKUs for all the items in the parcel. The Contents List is invaluable to your customers, as it allows them to locate items, without having to manually unpack orders.
This accelerates put-away for your customers, and ensures the traceability of items, leading to increased satisfaction in your supply chain.
As soon as the Delivery Label is printed, the order is booked for dispatch with the carrier. myCCL will then send the carrier and your customer a Delivery Note, detailing which parcel has which item and who packed the items.
Finally, you will be able to track the dispatch process of your goods on myCCL, with live milestone notifications updating your myCCL dashboard.
Talking of the Dispatch Solution, Ardtaraig’s Peter Mortimer said: “Try it, you won’t be disappointed!”