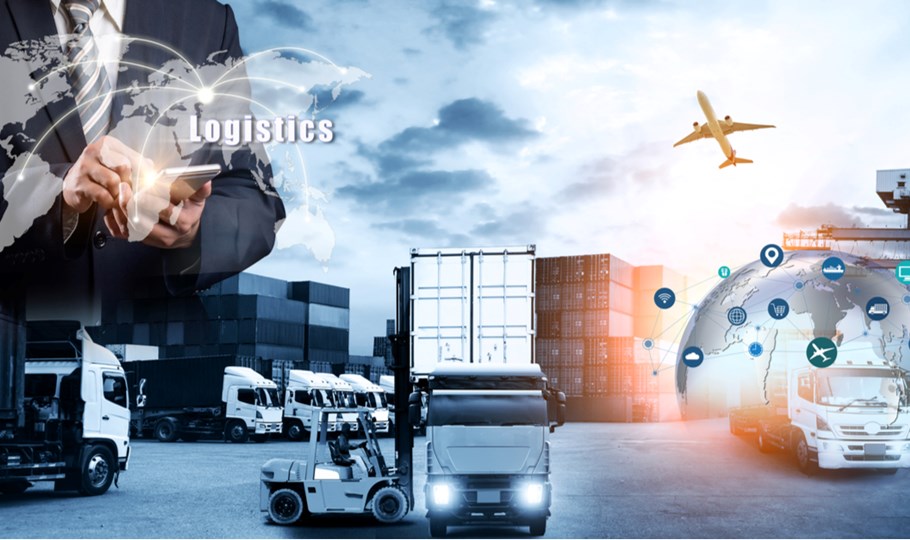
Tuning in to hear the latest supply chain insights, thousands of delegates logged on to the Logistics Business Show, from 15-17 March.
During the show, industry leaders tackled key topics including sanctions, driver shortages and Brexit. They then discussed the opportunities of digitalisation and sustainability. Here Julie Shennan, CCL’s Content Marketing Manager, recounts the key messages from the show.
The background issue of many panel discussions was the trade sanctions on Russia, being felt in different ways across every part of the sector.
Speaking at the Sustainable Low-Carbon Supply Chains panel, Kevin Onderbeke, Director of Business Development at Ahlers, explained that rail, sea and air routes around Russia are restricted, causing exporters to try to store goods or send them elsewhere.
He said: “In the long term we are suggesting people look at reshoring. We are looking at where our core customers and production units are located, to see if we can outsource production and do some contingency planning.”
Alternative solutions were also being sought for inbound logistic routes. Paul Williams, Executive Director at Woodland Group, suggested businesses should think outside the box.
He said: “Understand your inventory, and your movements of goods and stabilise them; it’s a better solution than resorting to expensive air freight with a high carbon burn.”
Increasing sustainability through improved business processes was also a recommendation of Michel Stekelenburg, Director of Strategic Accounts EMEA at Project44. Speaking at the Road Transport Challenges panel, he explained that digitalisation was key to this.
He said: “Technology must increase efficiency. Operational teams in carriers must not be constantly firefighting. People should sit with their end clients and figure out how they can get a more sustainable supply chain.”
Michel explained that, in road haulage, digital route planning can minimise void space and utilise backhaul, while more advanced technology can measure vehicles’ performance, all helping businesses reduce their carbon footprint.
Other suggestions from the panel were using carbon tracker solutions and electric vehicles to minimise CO2 emissions.
However, Tom Southall, Policy Director from the Cold Chain Federation, said UK road infrastructure must evolve to meet the electric vehicle demand.
He added: “Electric small goods vehicles are becoming more common in places like London, but HGVs are more of a challenge. We need the tech to be developed, for electronic vehicles to be more widespread and be backed up by the infrastructure.”
As well as better infrastructure for electric vehicles, the panel agreed that driver shortages were a big challenge to the future of road haulage.
Tom said: “We are seeing a huge churn, particularly in young drivers. So as an industry we need to take a longer-term look at how we tackle it.”
He suggested improving service station conditions, working patterns and pay, as measures that could help attract and retain drivers.
However, Andrea Martin, FreightViewer Coordinator, cautioned that pay increases would be passed to the consumer.
She said: “The issue can be covered by better salaries; however, this will increase the cost of goods for customers. This is a global problem, so we need to find a global solution.”
While the panel acknowledged that driver shortages were an international challenge, they also agreed that Brexit had further complicated logistics in the UK.
Tom said: “UK exporters have been hit hard, particularly those working in groupage. If you have 10 different types of goods in a lorry, then they all need to be checked.”
He added: “In January we started introducing import checks, from July there will be more detailed checks on things like meat and dairy, and this all adds costs and delay.”
With holdups at borders, driver shortages and sanctions, it has never been more important for supply chain professionals to save their team time by digitalising their operations.
Michel said: “When we talk to our clients, we can see how inefficient their processes are, such as using Excel, not AI or machine learning, so there is a lot to gain. If we can ensure that they automate their processes, then they can know about delays at the earliest stages possible, so they can communicate with their customers.”
As well as using automation in multi-carrier management software, panelists at the Business Logistics Show explained that modernising warehouse solutions was key to business growth.
Speaking at the Automation Systems in the Distribution Centre keynote, Oana Jinga, CCO and co-founder of BotsandUs, said: “There are a lot of efficiencies to be had in the putaway and the stock checking process.”
However, she warned that when businesses planned warehouse digitalisation, they should forecast future requirements.
She said: “People often deal with immediate problems, without even thinking about the required solution for even six months later, once they have more data."
Technology’s vital role in overcoming logistics challenges was a key theme of the Logistics Business Show, in March 2022.
This message rang true with CCL Logistics & Technology’s own experience in helping customers reduce costs and grow, through its multi-carrier management platform, myCCL, as well as its supply chain solutions and smart warehouse technology.